CASE STUDIES
KETO reverse engineers high pressure pump for refinery application
An alumina refinery in Queensland, Australia were operating an ENS 2-21 high pressure pump. The pump was not specifically designed for the particle size and speed requirements of this application. Consequently the pumps had a short wear life which meant high pump replacement and maintenance costs for the client.
CHALLENGE
KETO were tasked to re-engineer the ENS 2-21 for specialised use in this application. KETO assisted with the ongoing design, support and pattern changes to accommodate performance requirements.
Immediate problems found with the existing design included early diffuser failure, excessive wear to the 1st and 2nd stage impellers, and cracking of the volute. KETO engineers identified the stepped wear rings as a significant issue which contributed to heavy wear on both the impeller and to adjoining components, including the suction liner and the interstage 1st diffuser. Major recirculation loss was also occurring, resulting in a short impeller life.
-
INDUSTRY / APPLICATION
Mining & minerals
- Alumina
-
LOCATION
Queensland, Australia
-
CUSTOMER BENEFITS
- Improved mean time between overhauls
- Significant savings on spare parts, maintenance and labour
-
FEATURES
- Improved wear ring design
- Redesign of second stage diffuser and back cover
- Heat treated components
SOLUTION
The original pump design included stepped wear rings on the 1st stage and 2nd stage impellers. In the improved design the tapered wear ring, without steps, is employed on the 1st stage impeller, and a straight wear ring on the 2nd stage impeller. This extended the life of the pump by improving the control of water flow. The 2nd stage diffuser and back cover were redesigned to provide additional restraint in the case of catastrophic failure. All pump components were heat treated to enhance wear resistance. This assisted in making the volute, and other parts, less prone to cracking. The end product was a waste water pump which is both cost effective and intrinsically safe.Cross section of ENS 2-21 Pump showing the original arrangement
OPERATIONAL IMPROVEMENTS
The redesigned ENS 2-21 pump allowed better control of water circulation and longer wet-end life which improved pump efficiency and prolonged the life of the pump. The pump also improved mean time between overhauls, which gave our client significant savings on labour, maintenance and spare parts. Our client continues to use the improved ENS 2-21 over the old design more than seven years after the initial redesign work.Cross section of ENS 2-21 Pump showing the improved design
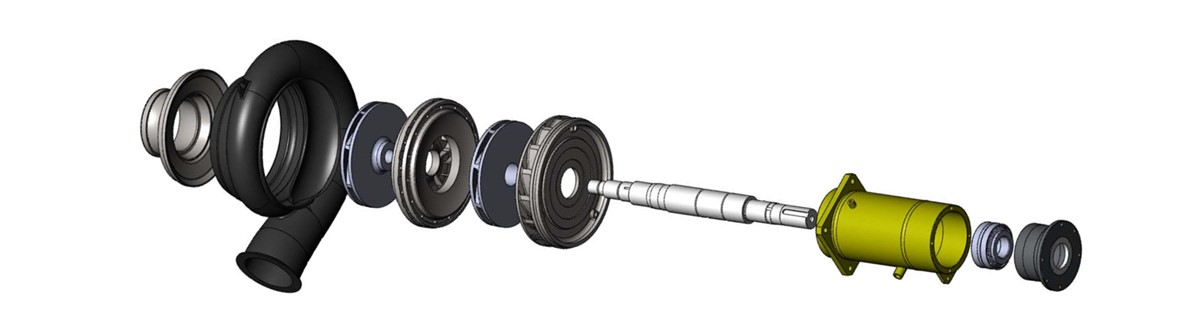
Exploded view of ENS 2-21 Pump
Downloads
-
Case Studies
KETO RE-ENGINEERS HIGH PRESSURE PUMP FOR REFINERY APPLICATION