CASE STUDIES
K-HEE™ impeller upgrade increases mill uptime
A copper mine in Canada was looking to maximise wear life of their impellers and improve shut-down intervals.
CHALLENGE
The site were using legacy design impellers which were dictating when the ‘mill shuts’ were scheduled. The site had impeller life averaging at 900 hours using legacy AH series parts and up to a maximum of 1,400 hours using expensive, specialised impeller materials. The mine had tried low cost replicas from various sources, but found that the resulting life (as low as 600 hours) combined with poor fits and performance, cost them substantially more in additional downtime than the savings made on the impeller price.
-
INDUSTRY / APPLICATION
Mining & minerals
- Copper Mine
-
LOCATION
Canada
-
CUSTOMER BENEFITS
- 600hr to 2,500hr impeller life increase
- Extended time between shut downs
- Spare parts savings over $76,000 CAD p.a. per impeller
-
FEATURES
- KETO K-HEE™ impeller
SOLUTION
To increase the life of the pump and increase mill up time, KETO engineers installed a KETO K-HEE™ 10G metal (WI05) into a legacy 12/10ST-AH pump. The K-HEE™ severe duty, high efficiency impeller incorporates high efficiency with low wear. KETO K-HEE™ impellers do not increase seal chamber pressure, do not increase thrust bearing loads and due to their severe duty design can be used in both fine and course slurry services and low NPSHR applications.OPERATIONAL IMPROVEMENTS
After 1,300 hours of operation, the wear of the KETO impeller was estimated at only 50% wear (image right). The KETO K-HEE™ impellers are consistently exceeding 2,500 hours life, which is over 4 times the life of low cost replica copies, 2.7 times the life of a legacy impeller and 1.8 times the life of a legacy impeller made of expensive materials. Using the K-HEE™ impeller, there is virtually no loss in performance and no premium material charge. KETO are now working with the client to extend the life of their volute liners.After 1,300 hours, K-HEE™ 10G impeller at 50% wear
FINANCIAL ILLUSTRATION
Due to this increased impeller life, there were significant parts and labour savings as well as increased plant availability. Spare parts savings alone are $76,903 CAD p.a. per impeller.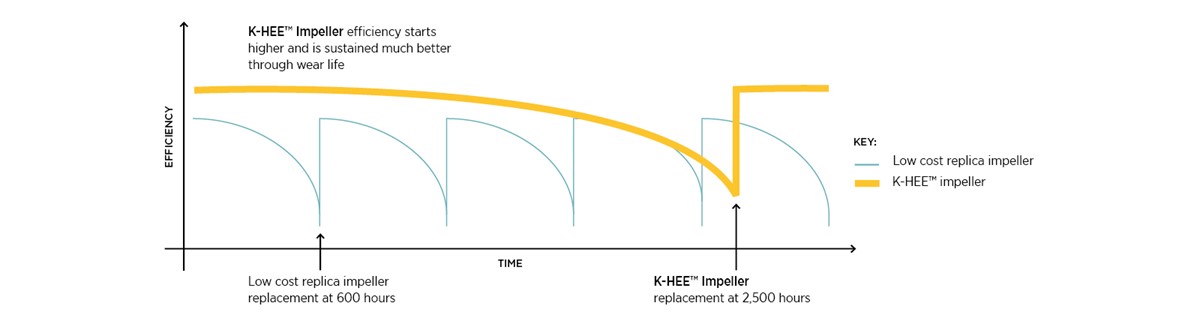